William Moore
Engineering Portfolio
A Showcase of William Moore's Work

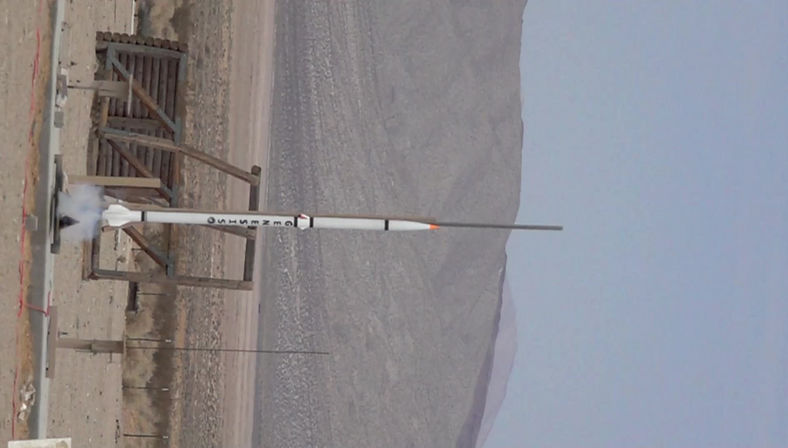

I have always loved creating things; the harder it is to build, the more I wanted to build it. From an early age, I showed interest in anything that moved, Trains, Planes, Cars, Rockets, and Boats, I wanted to learn how each of them worked. My love for space and flight spans from the fact that it's a challenge to even maintain the state of flight; it was a hard challenge to solve and overcome and so I needed to learn how it was done. Soon I was building any type of vehicle in any videogame that simulated them, and soon after, I started reconstructing my simulated projects into reality. I want nothing more than to explore the frontiers of humanity's challenges and build the vehicles that get us there.
Rocketry Work
LEGACY A-1
Q2 2022-PRESENT
The design of my Legacy class rocket started after the successful full flight of my Genesis rocket after I got annoyed with how purpose-built and un-modular amateur rockets were. So I set out to design my Legacy class rocket which was built ground up for modularity; the rocket would be split into two halves, payload and propulsion. This required me to design a new recovery system that only required the rocket to split at one interface but allow two separate deployment events. I relied heavily on my previous experience of 3D printing to create most of the structural elements, further allowing modularity and weight savings.
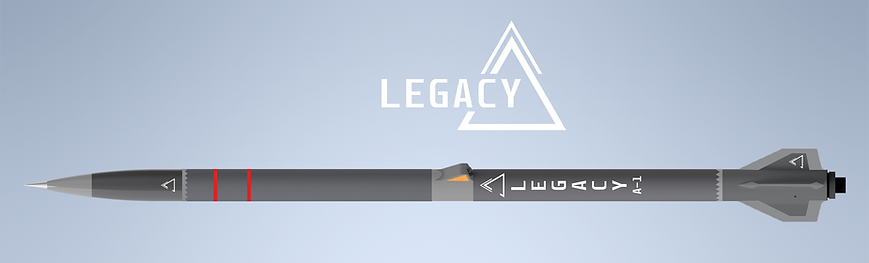
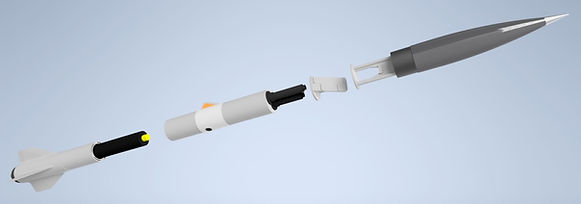
Legacy is a from-the-ground-up modular design, allowing the top half electronics/payload package and the bottom half propulsion/camera bay to be swapped interchangeably. In its current planned configuration A-1, it is set to carry 2kg of electronics and recovery payload to 2 miles of altitude. Hosting 3 independently armed commercial flight computers for a redundancy factor of 4, along with live downlinking of GPS location for efficient recovery and data logging. 2 cameras look towards the horizon and down towards the Fin-can for 2.7k recording of the launch. The recovery system uses CO2 gas to deploy chutes allowing for deployment at any altitude, unlike traditional black powder systems. The modularity of the design allows flights of 2kg of payload to fly to any altitude from 500ft to 4 miles in apogee and from speeds of Mach .3 to 1.75.
GENESIS
Q2 2021-Q3 2021
Genesis was my rocket purpose-built for my Level 2 Certification with NAR; I had decided to use the same diameter of fuselage as Sirius (2.6'') and to make the main structure out of longer fiberglass tubing. Because Genesis was going for an L2 Certification and reaching nearly a mile in altitude, I had to switch to a new dual-deploy recovery system along with a GPS locator for easier recovery. A camera facing aft was added to give video footage during the launch seen below.
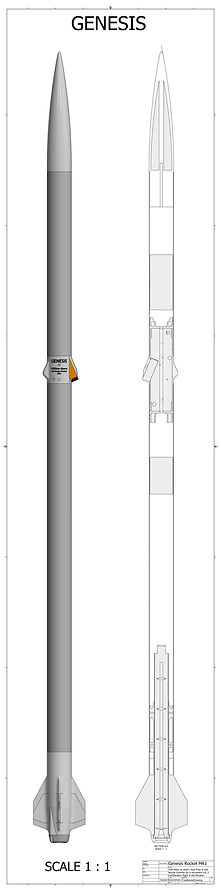

Genesis was named in part to its launching the summer before I started college and partly because this is what sealed the deal for me to become an Aerospace engineer. Genesis was my most complex design at the time; standing at 7ft tall, comprised mostly of 3D printed material and Fiberglass tubing, dual redundant dual deploy systems, Dual flight computers, a GPS tracker, and a Camera for flight recording.
​
Genesis flew first as a test flight to verify recovery systems and flight hardware in preparation for its goal flight in the Mohave. (Seen Left)
​
Genesis flew once more in the Mohave at the first Hot Nozzle Society event and reached its 1 Mile altitude goal, landing safely and was recovered successfully. (Seen Right)
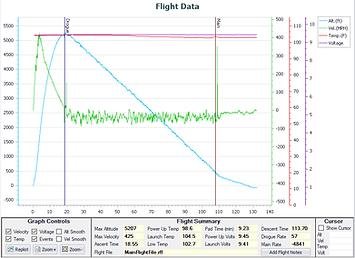
SIRIUS
Q1 2021 - Q2 2021
Sirius was my first rocket, designed to get me my Level 1 certification. I had just learned rocketry was a thing not but a month before building Sirius, and I was already trying to get certified in it. I had just gotten my first 3D printer, and when it came to the point where I had to mess with resin to glue flimsy balsa wood fins onto the rocket, I decided to 3D print the entire bottom section instead of getting my hands sticky, a novel idea at the time, the club owners that certified me said it was their first time seeing 3D printed structural components for rockets. The 3D printed Fin-can brought several bonuses to my design, those being: Lightweight, Endlessly producible, Un-breakable for the demands of a Lvl 1 rocket, and modularity.
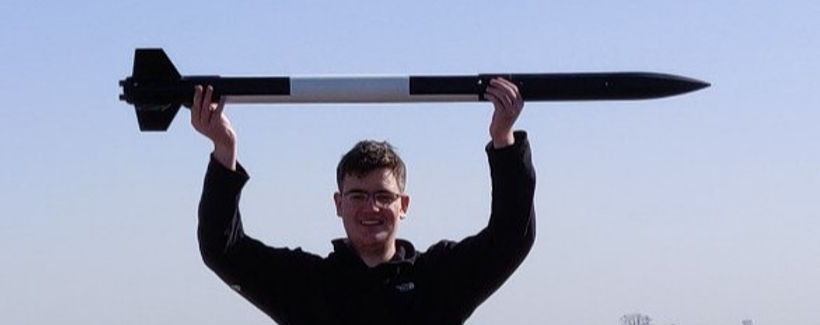

Sirius is named after the Brightest star in the sky, of which burns bright blue, just like the propellant chosen for its certification launch. It measured 4.5ft tall with a 2.6in diameter cardboard rolled fuselage. On its first flight, it flew on two F-class motors reaching an altitude of 1,500ft; this flight had no electronic payload. On the second flight, which got me my Level 1 Certification, it flew on a single H-class motor; this required a new Fin-can and showed the modularity of 3D-printed structures.
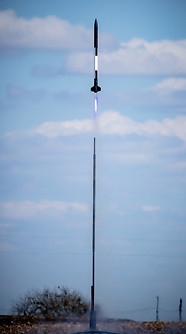
Other Work
MACHINING
While Studying at Austin Community College, I took Intro and Advanced CAM classes which had me working on Mastercam, Hass Super Mini Mills, and Hass Lathes, programming tool paths for generic, and my own Aerospace Designs. This taught me the basics of CAM software, Setup with Hass machines, and basic Machining techniques.
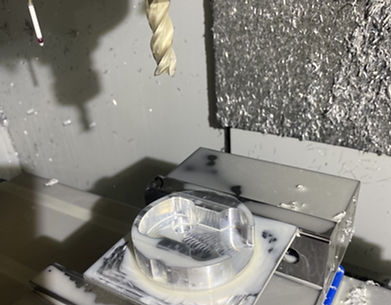
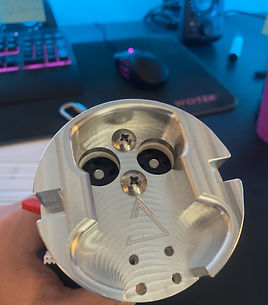
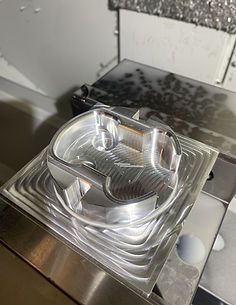
3D PRINTING
I have been FDM 3D printing for over 5 years, along with the maintenance, CAD work, and Slicer work that goes with it. Most of my 3D prints have been geared toward Aerospace applications, along with prototyping and bracket development. To fulfill the demands of my ever-growing rocket sizes, my stock Ender 3 Pro Printer had to get bigger, so I modded my 3D printer to print at a custom volume of 16x16x20in; this allowed me to print fin cans that had a Fin-span of up to 22in or full-sized helmets that can fit on someone's head.
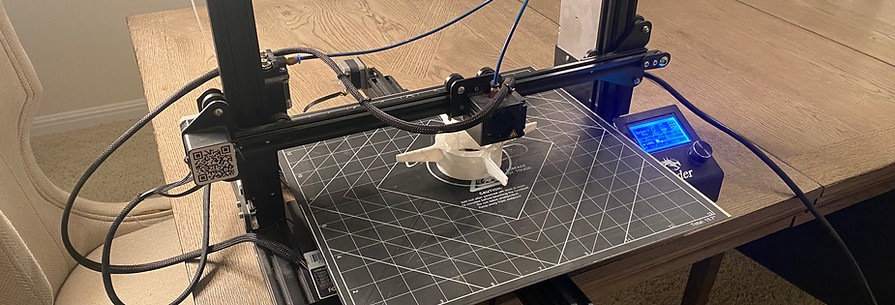
ELECTRONICS
Stripping, soldering, crimping, and wiring are all too common occurrences during the fabrication of my Electronics bays for my rockets. PCB fabrication has been practiced during the building of my Genesis rocket when fabricating the Egg Finder GPS module (seen right). Basic electronics work for Pc building, Car mechanical work, house renovation projects, and other projects like IR night vision goggles and learning electronics basics have allowed me to become experienced with everyday electric wiring needs on jobs and worksites along with tools like multimeters and wire strippers.
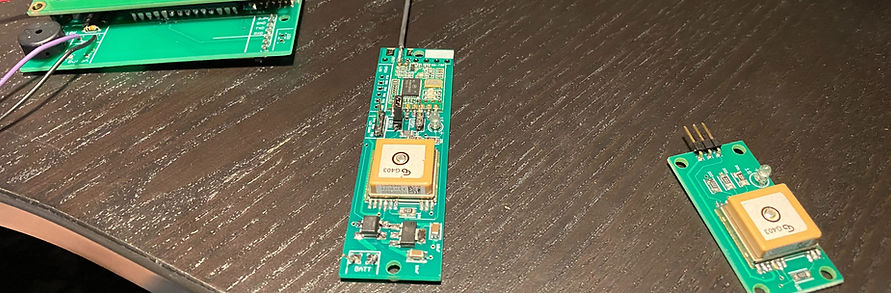
CAD DESIGN
Autodesk Inventor is my go-to cad software, learned through a combination of self-teaching and schooling. Most of my cad work surrounds Aerospace applications, along with some cad work for bracketing and furniture. For over 3 years, I have gained experience in producing CAD designs optimized for FDM 3D printing and learned techniques to fix common problems such as 'elephant's foot and the need for printed supports by designing in workarounds at the CAD stage, so parts fit seamlessly off the print bed saving time and money.
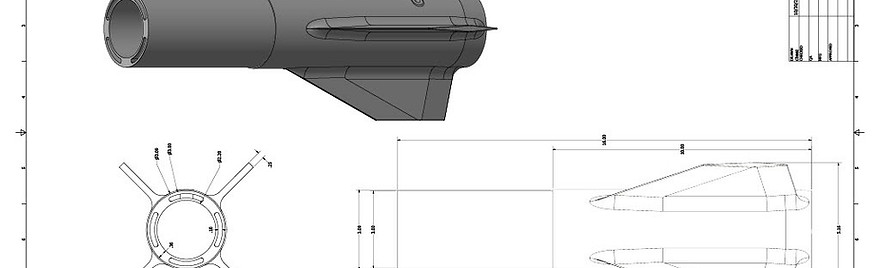
FURNITURE
My skills are not only useful for rockets; large furniture built from scratch allows me to flex my trade skills. Built from scratch using plywood and basic plans, this murphy bed allows me to fold away my mattress to give myself extra space for projects or to simply open up the room. This project helped me build shop skills and practice building large-scale structures using common hand tools.
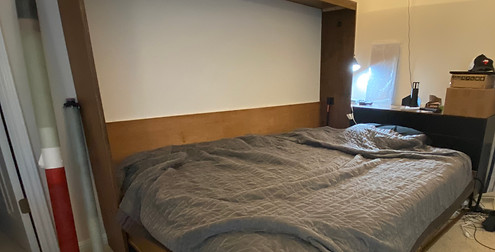
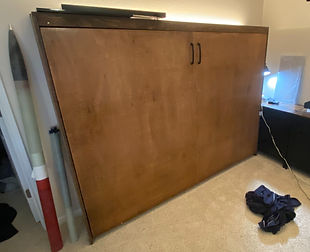
Hot Nozzle Summer 2021 :
This was the first ever Hot Nozzle Society event, I joined as a participant and flew my rocket Genesis for my Level 2 Certification at the event. The event took place in the Mohave Desert in California, on an old military testing ground, This launch site is where most University teams come to test flight hardware for their own Space shot projects. P.S. what they say about the desert being cold at night is true.
HOT NOZZLE SOCIETY WORK
Rocket Rodeo 2022 :
For this year's event, I was accepted to be Recovery Lead; I led a group of about 7 volunteers on recovery operations for attendees' rockets. I cooperated with drone operators to find and locate downed rockets in dense cornfields. I helped recover up to 7 vehicles, the farthest one away being over a mile away. This event took place in Austin, Tx, during a record-breaking hot weekend, so keeping attendees and recovery parties looked after and hydrated was my biggest priority. I assisted with the setup and tear down of launch infrastructure along with assisting the fire crew in operations whilst also maintaining and monitoring my recovery team's operations. I was able to work side by side with NASA and Lockheed employees and was invited by the former chairman of SEDS (Students for the Exploration and Development of Space) to join him in November for their annual convention.